June 29, 2020
Opened just six months ago, the Auto Innovation Centre is already making big impacts and expanding its services for the Australian Aftermarket.
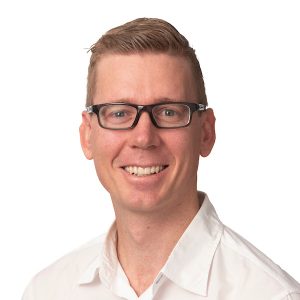
AIC Managing Director, Luke Truskinger
Since the opening ribbon was cut back in December, the Auto Innovation Centre (AIC) has been turning heads thanks to its specialised industry focus and customised service offerings.
Already many companies in the Australian automotive aftermarket industry – including but not limited to AAAA members – have been impressed by the Centre’s state-of-the-art facilities and the unrivalled role it can play in their product development activities.
“We are a very focused team and the Centre has been designed from the ground up to help the Australian Automotive Aftermarket industry,” AIC Managing Director, Luke Truskinger, explained.
“When you call the AIC, you talk to the people who not only work in the Centre but who played a key role in creating it. Our team has a broad range of experience in both the aftermarket and OEM automotive sectors, and this allows us to offer tailored and unique advice to those utilising our services.
“While the AIC is wholly-owned by and co-located with the AAAA, being a separate, independently-functioning business entity provides benefits to the entire Aftermarket industry.
“Our mission and ability to represent the industry as a whole allows us the unique opportunity to collaborate and gain traction (and all-important vehicle access) with OEMs; and we are pleased to offer cost-effective, premium services to our customers. We are committed to always demonstrating best practices as a true centre of excellence.”
Hand in hand with the AIC’s dedication to best practice and accessibility, is a core commitment to confidentiality. This means customers can feel confident in using the AIC for their most secret product development activities.
“Absolutely every interaction between customers and the AIC, right from the very first phone call enquiring about utilising the Centre, is completely confidential,” Truskinger said.
A COMPREHENSIVE ARRAY OF SERVICES
From the aforementioned access to vehicles to the use of the workshop for test fitting; 3D scanning and post processing; 3D printing; dynamic vehicle testing and ADAS calibration; the AIC boasts a comprehensive service offering to its clientele.
Vehicle access
“One of our points of difference is that we acquire vehicles which are then made available for companies to rent for the purpose of product development either on or off site,” Truskinger said.
“Access to vehicles is a real challenge for many companies because they can’t justify the expense of sourcing them; and while commercial ‘rentals’ can be a stop-gap this is far from ideal and usually, it is not permitted to conduct product development on hire cars.
“As a hub for the whole industry, we can acquire these vehicles for the benefit of all; targeting vehicles which are of particular interest to the aftermarket based on demand – even if they are not typical of accessorising.
“This means clients can come to the AIC and access vehicles for test fitting in our workshop, or they can arrange to rent a vehicle from us and take it off site for other types of dynamic testing.”
A fully-equipped workshop
Customers can also benefit from accessing the truly state-of-the-art workshop which is fully-equipped with all of the tools and equipment they could possibly need thanks to the Centre’s supporters.
“Thanks to the collective expertise of the industry, we have been able to fit out our workshop to make sure that virtually anything that could be done on a car, can be done here at the AIC,” Truskinger said.
“We are very thankful to all of our sponsors, partners and especially our champion companies (please visit www.autoic.com.au for a full listing) who have provided support since long before the AIC was guaranteed to be approved.
“They believed this was something which was going to help the industry as a whole and their backing has made the AIC a reality.
“Further, their continued support alongside our sponsors and partners ensures that not only are we offering world-class facilities now, but that we will continue to stay at the forefront of technology far into the future.”
Alongside a fully-fledged fabrication workshop which boasts Burson Auto Parts-supplied Hunter Equipment hoists, tyre changers and tyre balancers, as well as a full complement of Repco hand tools and Milwaukee power tools, the AIC has a long and varied list of precision equipment on-hand.
3D scanning, post-processing and printing technology
Amongst this equipment is a range of the latest 3D scanning, 3D post processing and 3D printing technologies.
“Having highly detailed and accurate 3D scan data is vital. In recognition of this, we have invested in two types of 3D scanning technologies, with each scanner performing a different function,” Truskinger said.
“This means we have the ability to scan entire vehicles, chassis and mechanical components as well as other items. This is thanks to metrology grade scanners which offer some of the highest possible accuracy available and produce data which exceeds the expectations of our customers.
“Of course we all know scan data itself is not overly useful unless it is post-processed well, so the AIC has a number of post-processing programs which allow us to produce surface and solid models to suit the customer’s chosen usage and CAD programs.
“As part of the AIC’s commitment to help customers amortise costs where possible, companies can even purchase 3D scan data created by the AIC as standard data sets which have been organised into particular target areas to suit most common requirements.
“At the same time, we offer pay per use contract scanning services and, like with all activity undertaken by and for customers at the AIC, the customer owns all of the data for that job – although they can agree to allow the AIC to use or adapt their data for industry access in exchange for lower cost service if they choose to.
“Then there is our additive manufacturing centre, which boasts three 3D printers which offer three different technologies and therefore three different capabilities. We have done this because each printer has a unique strength: one is best for larger volumes, one excels with incredibly detailed smaller parts, and one is perfect for very strong parts.
“This means we can provide a more flexible service offering which is better suited to the customer’s application. We are also getting ready to run training courses on additive manufacturing to help keep the industry abreast of the new technologies and even help them to add additive manufacturing capability to their own company if they so wish.”
Dynamic Vehicle Testing and ADAS Calibration
When it comes to the various systems of vehicles on the road today, the AIC is ready to assist with dynamic vehicle testing and Advanced Driver Assist Systems (ADAS) calibration offerings.
“We are proud to offer dynamic vehicle testing services with a range of specialised equipment including a steering robot, inertial measurement units, GPS positioning technology, force transducers and data logging equipment,” Truskinger said.
“We are an approved testing facility for ADR 31, 35 and 88 which represent brakes and electronic stability control and we also offer customised dynamic testing services tailored to the requirements of the customer.
“AIC sponsor, Continental, plays a key part in this area of dynamic testing, supplying all of our tyres and tyre data for future simulation work.
“With the widespread introduction of cameras and radars into new vehicles, it is also exceptionally important that we are able to support the industry to best understand the operation and performance of that technology and the impact after accessorising.
“As such we are thankful for our partnership with AIC sponsors Bosch and Hella Gutmann Solutions, which allow us to offer a full complement of ADAS calibration equipment.”
Training facilities
The Centre also boasts a fully-fitted out training facility which can now be used for training courses, seminars, networking events and more (pending any physical contact restrictions.)
“Where previously you may have booked a hotel meeting room or similar for your seminar or training event, the AIC’s facilities allow you to take advantage of not only a state-of-the-art training room, but one that is accompanied by the AIC workshop,” Truskinger said.
“This means those hiring the room can arrange for the use of the workshop to accompany the training space so they can perfectly partner theory and practice for their event. Even if the workshop is not utilised, the view is great.”
Even more services are coming soon
And that is not all, with a number of other exciting services also coming to the AIC during the third quarter of 2020.
“Soon we will have a range of exciting new equipment at the AIC,” Truskinger explained.
“We will be switching on our hydraulic test facility which can perform asynchronous fatigue testing and static testing up to 10kN.
“We will also be offering vibration testing with load capacity up to 150kg which can provide high frequency vibration testing to validate the durability life of components mounted to a vehicle chassis or engine.
“At the same time, we will be bringing to the AIC laboratory-spec tensile/compression testing with capacity up to 10kN and a range of options for grips and mounts.
“Finally, we will also be introducing a Damper Dynamometer which will boast the capability to provide highly accurate damper plots for a wide range of vehicle dampers, right up to armoured.
“It really is an exciting time for all of us here at the AIC and we look forward to offering these new services and continuing to evolve and exceed the expectations of the industry.”
This article was originally published in the June Australian Automotive Aftermarket Magazine.